Artisanal blacksmiths in Malaysia build up strong following with traditional skills, modern techniques
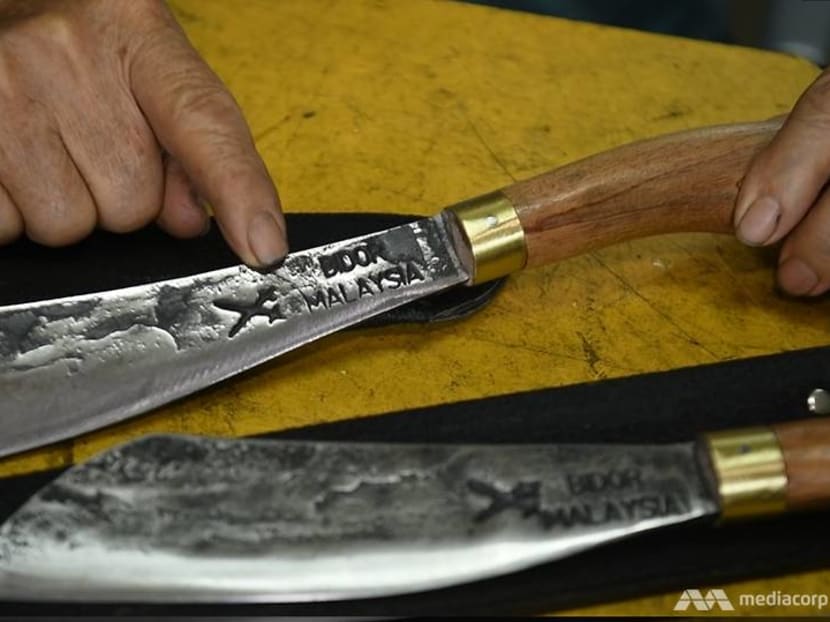
The trademark crossed swords, as well as the "Bidor" and "Malaysia" etchings have made Kwong Yuan Loong's blades famous both locally and overseas. (Photo: Vincent Tan)
BIDOR, Perak: In the storeroom of Kwong Yuan Loong smithy, stacks of blades were wrapped in newspaper, the smell of machine oil still fresh after workers applied a coating to prevent the high-carbon steel from rusting.
The sounds of hammering reached through even with the metal shutters rolled down, as Chin Pin Yon, 79, sat down to recount the history of the smithy founded by his father in the late 1920s.
“Back then, the workshop was just a shop in the Chinese village. And we were forging our cutting implements there until we moved out in 2000.”
“The reason was because of the noise. The place became a new village, and people were living next door, so the hammering got very loud,” said Chin, himself suffering from partial deafness after over 50 years at the forge.
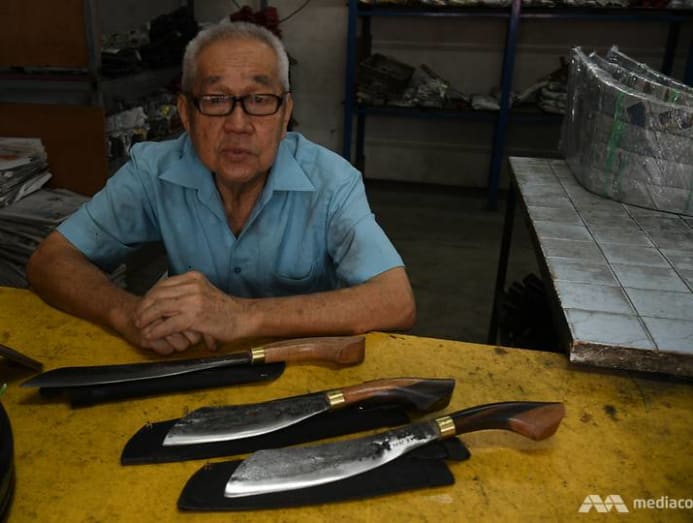
If the brand “Kwong Yuan Loong” does not ring any bells, the moniker “Bidor parang” might, along with the crossed swords logo and toponym “Bidor” etched on their duku candung and golok knives (variants of the parang).
Parang candung, a blade design originally from Sarawak, is popular both locally and overseas as an outdoor implement, and more so the Bidor-made parangs, as an affordable and reliable cutting tool.
For people who use parangs, either in the agriculture industry or the outdoors, Bidor in Perak is synonymous with parang making. And it is not uncommon for walk-ins to turn up at Kwong Yuan Loong to specifically purchase their parangs.
However, the smithy, now operating as a factory, makes more than just parangs.
“Actually we make agriculture cutting tools, like blades for tapping rubber trees, others for harvesting bunches of oil palm fruit, and also durian knives,” said Chin.
READ: Preserving Malaysia’s traditional houses, one pillar at a time
Across Malaysia, countless traditional blacksmiths toil to make cheap tools and agricultural implements for their local communities.
Kwong Yuan Loong used to be one such smithy starting out, and while it still keeps a focus on traditional blacksmithing, it has also incorporated new technologies and production methods to keep in step with the times.
The strong demand, both from local and international clients, is a testament to the quality of its products.
Meanwhile, the industry has also witnessed the emergence of new blacksmiths who take pride in producing high-end, artisanal knives with new techniques and materials. One such maker is Faris Zulkifli's Fursan Blades in Kampung Melayu Subang, Selangor.
Of these 20-odd modern artisans across Malaysia, a few have also garnered an international following among collectors and outdoor enthusiasts.
BIKING FROM PERAK TO PAHANG
Initially, Kwong Yuan Loong did most of its business in Pahang, although orders would also come in from other states.
“There’s a lot of agriculture going on in Pahang, so I would ride a motorbike there from Bidor ... we did not have a car, so I’d carry about 50 rubber tapping knives at one go.
“One hardware shop would take five to 10 knives or so. After you sold to a few shops, you’d have already finished your load, so we slowly built up from there,” said Chin.
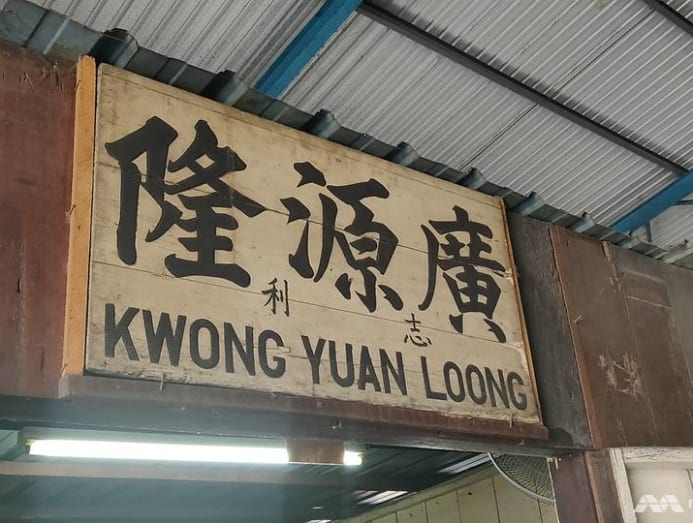
Chin said the smithy's blades only carried the crossed swords trademark back in his father's time.
“People wouldn’t know where to buy parang, so when I took over, I knew that if we wanted to market our product better, we must put the ‘Bidor’ name as well,” Chin recalled.
As the knives became more popular, some were also exported overseas.
“A lot of users overseas were happy with the knife, according to the feedback, but they didn’t know where it’s from, so our exporter asked us to add the ‘Malaysia’ etching. Now our most famous knife is the duku candong, and when the users come to Malaysia, they know where to go,” he added.
READ: 'I hope the deceased will receive these items’ - Penang paper effigy apprentices passionate about their craft
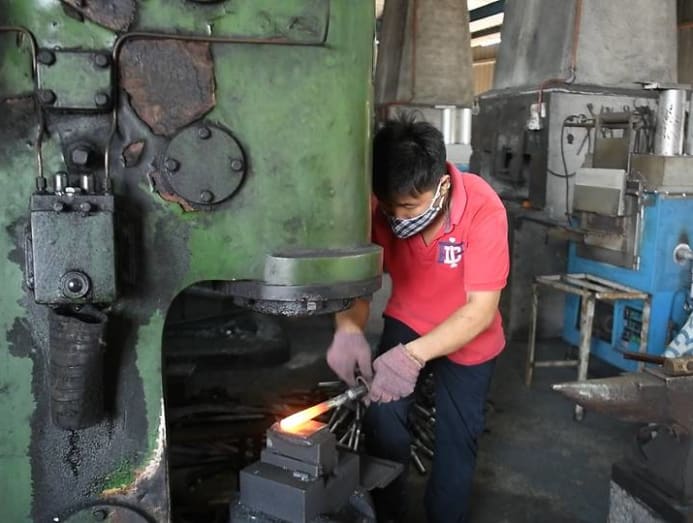
Apparently hand-forged knives were a big hit with Western visitors, and some came over to test the factory’s blades’ reliability and strength.
“Some tests even involved dropping the blades from a height to see whether they would break, and the visitors also came to see us hand-forging the blades,” he added.
The factory works mainly with an outdoors shop in Penang to market their parangs overseas.
“It started from there, and we get orders from both the Penang shop and individuals, but I can’t take on too many orders otherwise our order book would be swamped,” Foo Yoong Ming, who is Chin's son-in-law, said.
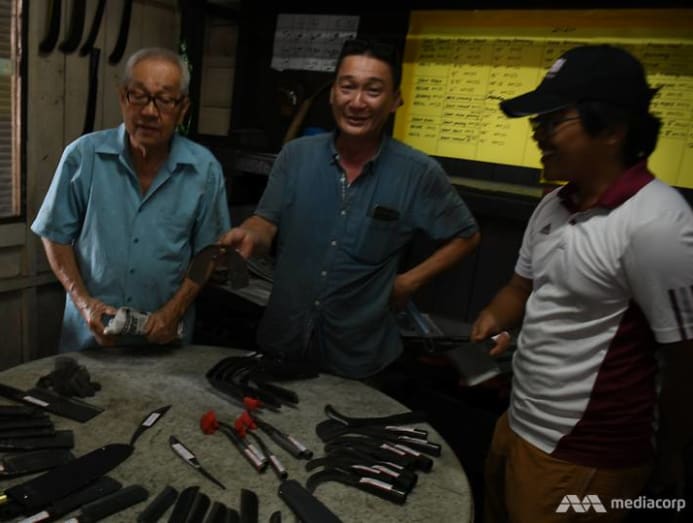
Among traditional parang makers, recycled leaf spring plates salvaged from vehicles were previously the preferred raw material which they could melt down and use. Land Rover leaf springs were traditionally considered "the best".
Nowadays though, the factory uses imported steel plates which are mill-produced, which are of much higher quality than recycled vehicle parts.
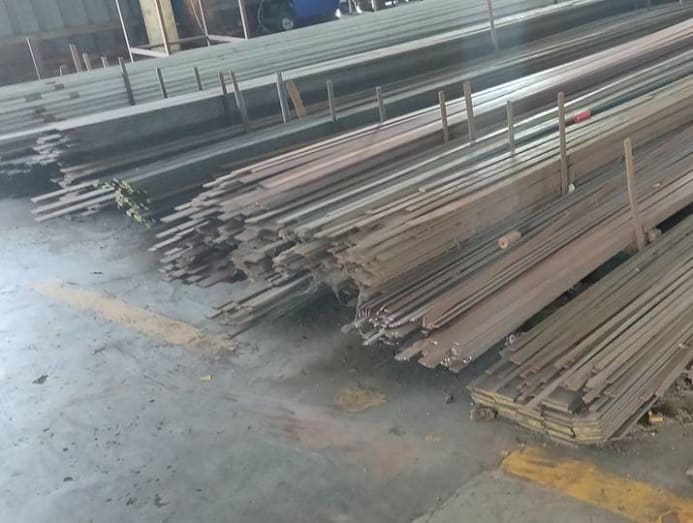
PART OF THE NEW WAVE
Meanwhile, over in the new workshop of Fursan Blades in Kampung Melayu Subang, Faris watched carefully as a piece of steel slowly heated up and glowed from a dull red to a bright colour inside his cylindrical forge.
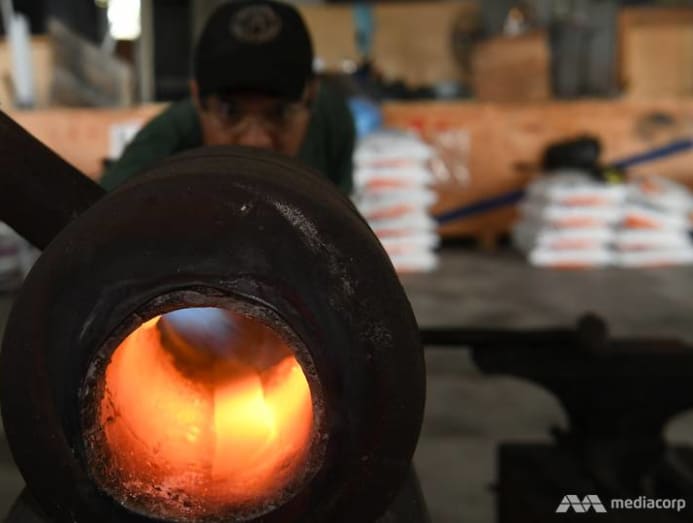
Once it turned cherry red or so, he deftly carried out the now-malleable steel piece, soft enough that he could hammer into his desired rough shape for a knife.
It takes Faris a few rounds of heating and hammering for his steel piece to take the desired flatness.
Forging carbon steel, a very basic tool steel, yields knives with a "raw" and "traditional" look that appeals to fans of such.
READ: Adopt a sun bear or terrapin - Wildlife conservationists in Malaysia appeal for donations to ride out COVID-19 impact
These days, however, there is more demand from users for the modern "super steel" type of knives made of powder steel and high-end stainless steel, which do not require forging and are less-prone to error.
He makes mostly outdoor and everyday carry knives.
For these knives, Faris usually employs the stock removal method, where he uses plates of steel sourced from a steel mill. After outlining the blade’s profile and form on the steel plate, he takes the steel bar to a belt grinder and grinds away the excess metal until he attains his desired shape and profile.
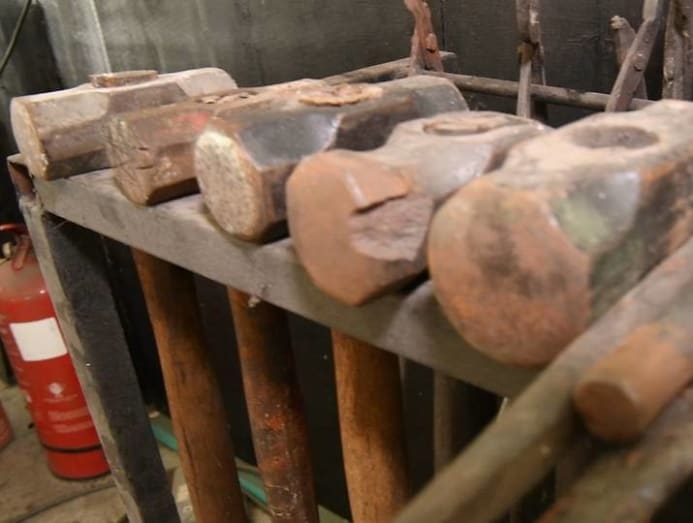
“You grind the bevels and other details, and then you send it for heat treatment to get the desired hardness then you finish it with polishing and so on,” he explained.
READ: COVID-19 lockdown stimulates Malaysia's retail investor boom
Faris, whose interest in blade drove him to become a professional chef, started Fursan Blades nearly seven years back.
Starting with scrap metal at first, Faris made many mistakes before learning how to make blades properly from other knife makers who were working with higher-end steels.
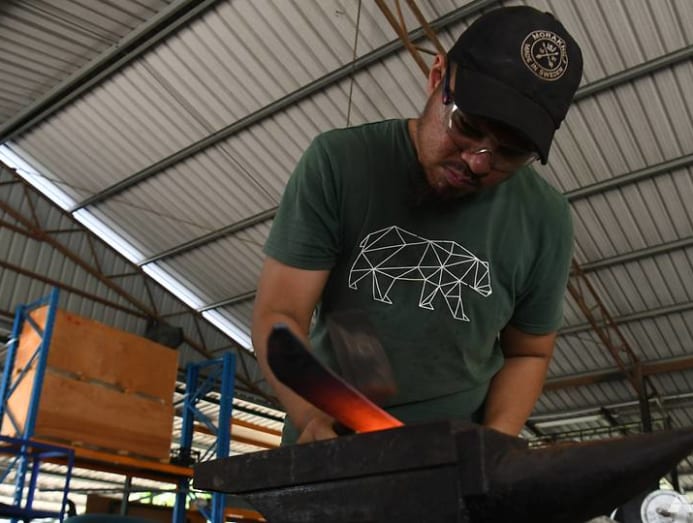
A normal day at work for Faris means making himself a cup of coffee and then planning out the day’s tasks, from cutting out the profiles for perhaps 10 knives at a time.
“I’ll be grinding the plates down all the way for three to four hours with these two machines, and if any of the knives are ready for their heat treatment, I’ll send them out.”
“I’ll have more than 20 orders easily at any time that I need to complete, and about 40 to 50 pieces which I finish in a month,” he said.
Faris also does special custom orders such as swords for display, as well as kitchen knives as a nod to his culinary past.
“For customised kitchen knives with supreme steel and good grinds, I make them by drawing on my previous kitchen experience.”
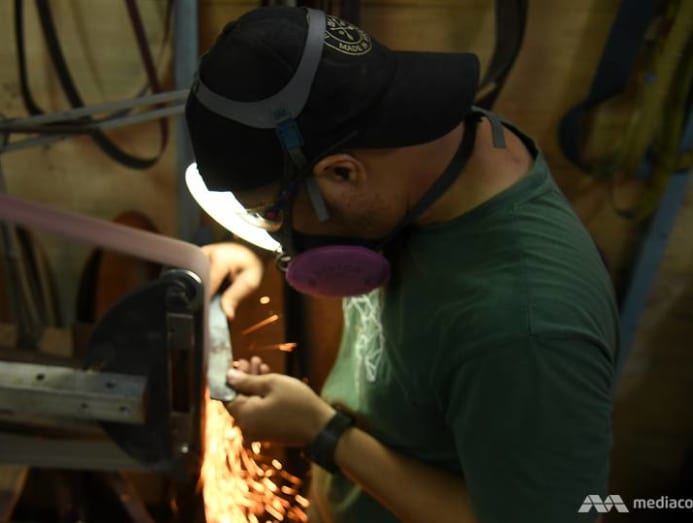
For Faris, it’s important to know how to use a tool like a knife or parang before making the proper tool for it.
“Right now, I’m also a student farrier (a blacksmith who works with horses) and I’d like to learn how to make the tools to change the horse’s shoes and how to do it.”
“You have to train and understand the process before you attempt to make your own,” he added.
THE NEED TO KEEP UP-TO-DATE
Both blacksmiths agreed that there is a need to keep their knife making skills and processes up-to-date.
Kwong Yuan Loong's Chin, who has handed the factory's management to his son-in-law over a decade back, felt that the factory would need to improve on its artisanal blade making with modern technology.
“Take quenching the blade after heat-treating it, you can’t just go by your eye, you also need instruments to read the temperature,” he said.
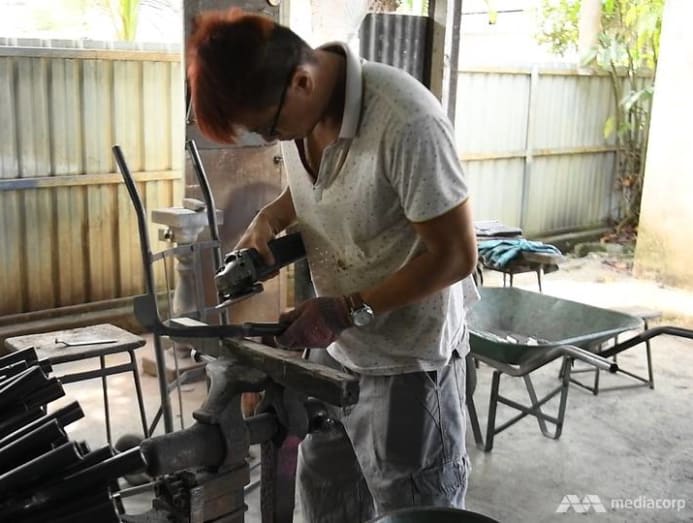
Besides transitioning from recycled or scrap steel, Foo's son, Er Xian, 24, explained that the factory had also gone on to use gas-powered forges instead of charcoal due to difficulties in sourcing the material. While the workers still apply the finishing touches by hand, there are also power hammers to help with forging.
Foo, 54, told CNA that blacksmithing was something of a sunset industry.
“But at the same time, people are also looking for artisan work, so I try to maintain hand-forging, but I’m also looking at increasing my machinery and output,” he said.
Nonetheless, Chin still wanted the younger generation to learn hand-forging from experience. "Because it’s not something you can get from books.”
READ: Fit for royalty - Malaysian Queen passionate about reviving Pahang handwoven fabric
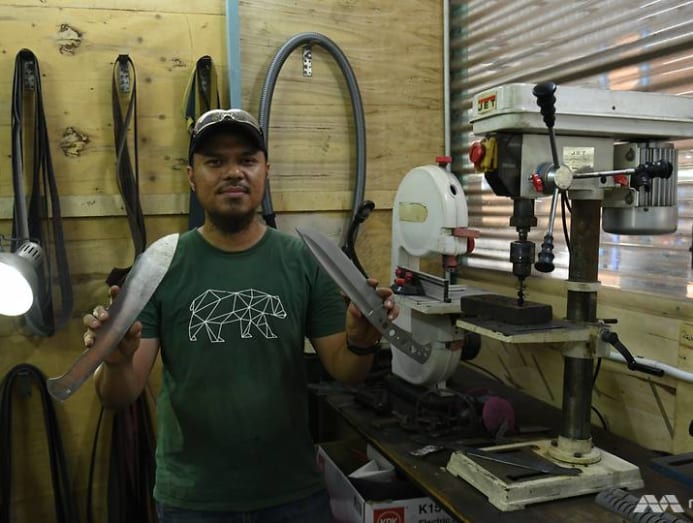
For Faris, what set modern knife makers apart from the traditional smiths was the clear documentation and scientific way of making blades.
Makers who employ the modern approach will be able to tell the customer upfront what steel they are using, the metallurgical composition of the steel and how long the knife’s sharpness is estimated to last.
“But since 2012, 2013, a lot of traditional knife makers have also been upgrading themselves, from modernising their forges to using better steels. I’d like to think that we somewhat inspired them to catch up with the modern knife industry."